Characteristics of Eonyx Granite Cutting Segments
1. The diamond segments possess good sharpness and high efficiency during the process of cutting, as well as long lifespan.
2. Good cutting result: smooth cutting, flat surface and even size.
3. Stable cutting and narrow cutting gap to ensure minimum stone waste.
4. Various segment shapes available: M shape, K shape, Taper shape, Flat shape, T shape, U shape, etc.
5. As a professional supplier, we can guarantee competitive wholesale price and stable quality.
6. Production capacity: our professional factory can supply 90000 sets/month.
7. Matured formula designing and testing system.
Diamond Segment Size
In theory, the length of the diamond segment should be designed taking into account the diameter of the saw blade, the number of diamond segments, the height of the diamond segment, the thickness of the diamond segment, the width of the nozzle, and the use parameters of the saw blade. In general, the shorter the diamond segment, the larger the number, and the narrower the nozzle, the better the coherence of the cutting, the better the cutting effect, the longer the cutting life, but the lower the sharpness. The length of the large saw blade diamond segment is mostly within the range of 20~25mm. When designing the height of the diamond segment, it is necessary to take into account the thickness, substrate quality, life requirements and cost requirements. The height of the diamond segment of large saw blades is mostly 10~20mm.
The thickness of the diamond segment should be determined according to the thickness of the base body and the wear ratio of the height and thickness of the diamond segment. Ideally, under certain cutting conditions, when the height direction of the diamond segment is finished, the dimension in the thickness direction is also flush with the substrate. When cutting highly abrasive materials, the thickness of the saw blade diamond segment should be larger, and the base should also be thicker; for cutting weakly abrasive or particularly brittle materials, the thickness of the blade diamond segment should be smaller; the blade diamond segment is too thick. Then the cutting resistance, cutting power and slit width will increase, resulting in waste of stone and energy. If the diamond segment is too thin, the abrasive layer will not be finished, and the thickness direction will be level with the steel substrate, which is easy to cause saw clipping and make the saw blade unusable. The thickness of the large saw blade blade should be 2~3mm larger than the thickness of the base.
Diameter (mm) | Diameter (inch) | Steel Core Thickness(mm) | Segment Dimension (mm) | Segment Number |
---|---|---|---|---|
300 | 12″ | 2.2 | 40×3.2×10(15,20) | 21 |
350 | 14″ | 2.2 | 40×3.2×10(15,20) | 24 |
400 | 16″ | 2.6 | 40×3.6×10(15,20) | 28 |
450 | 18″ | 3.0 | 40×4.0x10(15,20) | 32 |
500 | 20″ | 3.0 | 40×4.0x10(15,20) | 36 |
600 | 24″ | 3.6 | 40×4.6×10(15,20) | 42 |
700 | 28″ | 4.0 | 40×5.0x10(15,20) | 50 |
800 | 32″ | 4.5 | 40×5.5×10(15,20) | 57 |
900 | 36″ | 5.0 | 24×7.0/6.2×13(15,20) | 64 |
1000 | 40″ | 5.0 | 24×7.0/6.2×13(15,20) | 70 |
1200 | 48″ | 5.5 | 24×7.4/6.6×13(15,20) | 80 |
1400 | 56″ | 6.5 | 24×8.4/7.6×13(15,20) | 92 |
1600 | 64″ | 7.2 | 24×9.2/8.4×13(15,20) | 108 |
1800 | 72″ | 7.5 | 24×10/9.2×13(15,20) | 120 |
2000 | 80″ | 8.0 | 24×11/10×15(20) | 128 |
2200 | 88″ | 9.0 | 24×11/10×15(20) | 132 |
2500 | 110″ | 9.0 | 24×12/11×20(30) | 140 |
3000 | 120″ | 9.3 | 24×13/12×20(30) | 160 |
3500 | 140″ | 9.5 | 24×13.5/12.5×20(30) | 180 |
Other specifications are available upon request. | ||||
Silent and non-silent blades are available for choice. |
Design of the number of “sandwich” layers and the thickness of the hard layer.
Generally speaking, if the number of “sandwich” layers of the diamond segment is small and the hard layer is wider, the sharpness will be poor, while the number of layers and the hard layer are narrower, the sharpness will be better, but it may affect the cutting life. For the stone with fine grain, fine structure, high hardness and high toughness, the diamond segment should use more layers and a smaller thickness of the hard layer, while cutting the stone with coarse grain, loose structure, soft and brittle stone, A smaller number of layers and a larger hard layer thickness should be used.
In terms of the three dimensions of the size of the large saw blade diamond segment, the length direction is mostly 22~24mm. Generally speaking, the shorter the length, the better the sharpness is. On the contrary, the longer the length is, the better the life is. Under the same conditions of other parameters, the cutting efficiency of the 22mm diamond segment will be higher than that of the 24mm diamond segment. The height direction is mainly selected according to the processing object. Generally, the height of stone with high abrasiveness or long processing time is about 10mm. For conventional granite, the height is often between 15 and 20mm. The width direction is mainly related to the thickness of the base body, ensuring that the side gap between the welding surface of the diamond segment and the base body is about 0.6mm, so as to protect the base body from being worn by the processing object. Therefore, for stones with high abrasiveness or long processing time, it is necessary to appropriately increase the thickness of the diamond segment, generally to 8~10mm. The table below is the size of the diamond segments of common large saw blades for processing granite.
Application of Diamond Segments
For 300mm-3500mm saw blades, diamond frame gang saw blades, diamond core drill bits, diamond grinding cup wheels and different machines (multi blade cutter, gang saw blade, bridge cutting machine, single arm cutting machine, manual handing machine, able cutting machine, etc.) Diamond segment types include sandwich segment, multi-layer segment and orderly arrayed segment and carbide tips, every type is designed for various hardness stone (soft, medium hard and very hard stones) cutting: granite, marble, sandstone, onyx, limestone, travertine, quartz stone, artificial stone, andesite, volcanic, lava stone, basalt, microcrystal stone, blue stone, dolomite and construction materials (concrete, tile, ceramic, asphalt, floor) to reduce segment cost and increase cutting efficiency.
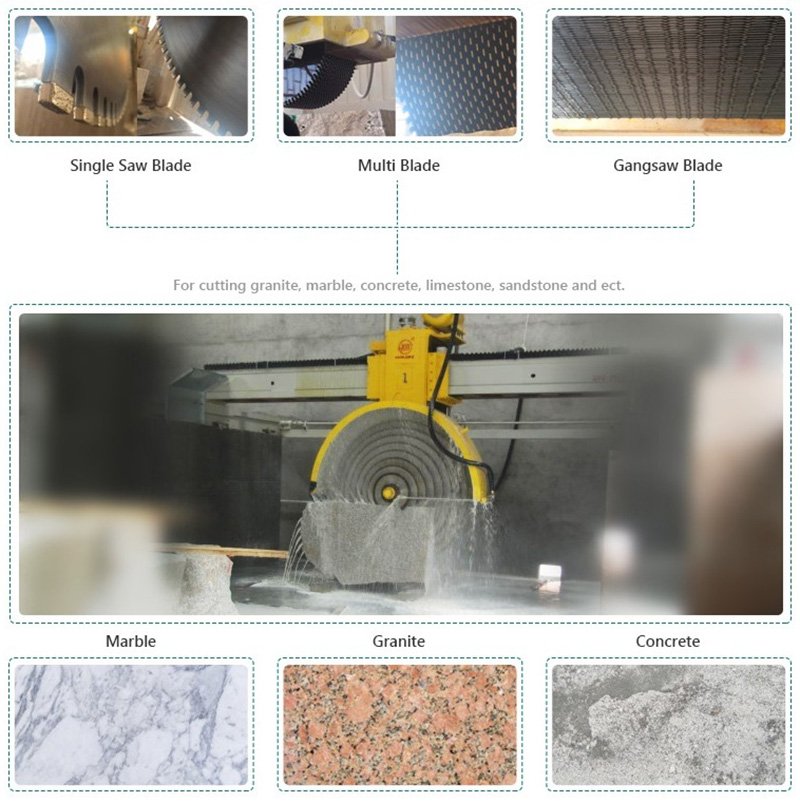
Packaging and Shipping for Granite Cutting Diamond Segments
One set of diamond segments packed in 1 box, 10 boxes in a carton and then cartons packed in crate. Besides the diamond segments could also be packed according to your specific request.
Rust proofed before packing – Water proofed – Impact protection.
Urgent order with less weight or samples, courier service is recommended;
Normal (regular) order which weight over 45kgs, delivering by air is recommended;
Big diameter saw blades or heavy weight products, shipping by sea is recommended.
Eonyx will offer advices according to the actual order requirements.
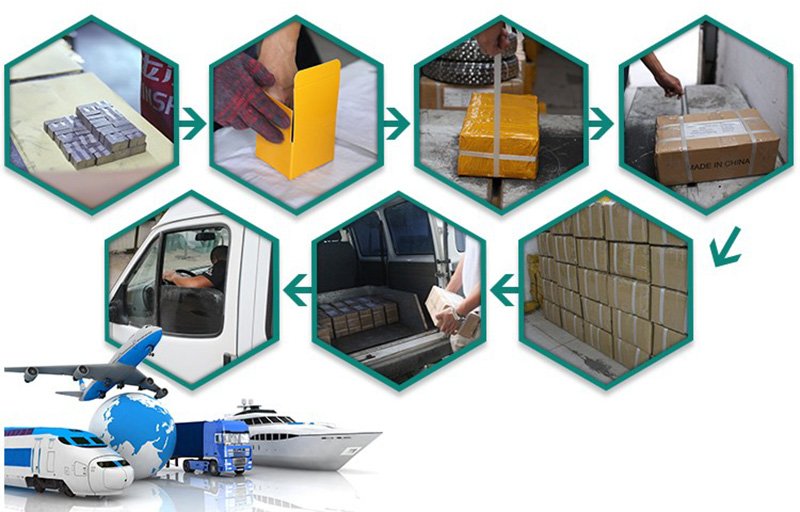
Selection and use of diamond segments and saw blades for stone
Correct selection of large saw blades
Under certain cutting conditions, diamond and matrix are the main factors that affect the use effect of saw blades. Secondly, the structure, size, matrix, manufacturing process, and precision of the diamond segment also have a great influence. “Choosing the right model for cutting” is the general principle for selecting a diamond saw blade, that is, the parameters of the selected saw blade (mainly referring to diamond quality, particle size, concentration and matrix formula, density, strength, hardness, wear resistance) and diamond segment structure, size, base material, base structure size, saw blade accuracy, etc.) should be adapted to the composition, hardness, and abrasiveness of the material to be cut, and the cutting machine and cutting parameters in order to achieve the best cutting effect.
Rational use of large saw blades
Install correctly
Correct and high-precision installation is an important guarantee to ensure that the saw blade runs smoothly, does not generate vibration, and gives full play to the cutting effect. When using, it is required to ensure that the cutting edge direction of the saw blade is consistent with the rotation direction of the main shaft of the cutting machine. Make sure the verticality of the saw blade and the main shaft of the cutting machine, and select the flange with the appropriate diameter. If the flange is too small, the end face of the saw blade will swing greatly during use. If the flange is too large, the spindle will increase the hanging weight, increase the runout, and reduce the depth of cut. Therefore, the circular runout accuracy of the saw blade and flange must be ensured.
Rational use of diamond saw blades
First, the use of coolant
When cutting, there will be friction and impact between the saw blade and the stone, which will generate a lot of heat on the cutting surface. The stone has poor heat dissipation, so that most of the heat is absorbed by the saw blade, and the diamond segment is the first to bear the brunt. In this way, it is very easy to cause graphitization of diamond, and the diamond segment is easy to burn and fall off. At the same time, the steel matrix is easy to be thermally deformed and cracked from the root of the nozzle. Continuously spraying a large amount of coolant from the front and back and both sides of the saw blade to the incision will play a good role in cooling and protecting the saw blade. diamond segment and base. In addition, if emulsified coolant is used, the hydrophilic and lipophilic properties of the emulsifier can make the surface of the saw blade and the rock adhere to a layer of lubricating oil film, which can reduce the friction coefficient during sawing, thereby reducing cutting resistance and vibration.
Cooling water is generally selected from cooling water, or an appropriate amount of rust inhisegmentor and an emulsifier (a hydrophilic and lipophilic emulsifier such as saponified dissolved oil, swire oil, etc.) can be added to the cooling water. Cooling water should be soft water without sediment, especially when cutting materials that will produce sticky and corrosive chips. In addition, care should be taken to use a reasonable coolant flow.
Second, line speed
The linear speed of the diamond circular saw has a great influence on the cutting. Studies have shown that when the linear speed of the saw blade is too low or too high, the wear of the diamond diamond segment will be accelerated, which will accelerate the abnormal wear of the saw blade and reduce the cutting efficiency. This is because when the cutting speed is very low, the contact time between the diamond segment on the saw blade and the material increases correspondingly during each cutting, which intensifies friction, increases heat, and deteriorates heat dissipation and cooling conditions, which aggravates saw blade loss. If the linear speed is too high, the cutting depth of a single grain of diamond per unit time will decrease, and the friction and wear of the rock on the diamond will be reduced, but at this time, the dynamic load of the interaction between the diamond segment and the material to be cut will increase, which not only makes the diamond mechanically affected. The loss of impact increases, and at the same time, the loss is also increased because the diamond is easy to break and fall off. The harder the material to be cut, the lower the linear speed of the saw blade, and the softer or more abrasive the material to be cut, the higher the linear speed. Under certain other conditions, there will always be an optimal linear speed for the diamond circular saw blade.
Third, suitable cutting productivity
Cutting productivity or cutting efficiency is the product of the cutting depth of the saw blade and the feed speed, that is, the cross-sectional area of the material cut per unit time. Practice has shown that for the same material, increasing the cutting depth and feed speed at the same time can improve the cutting productivity, but the abnormal wear of the saw blade will also increase, the service life will be reduced, and the sawing power will also increase, so the cutting efficiency is increased. cost. In the case of a given cutting productivity, the size of the feed speed also has a great influence on the wear of the saw blade. If the feed rate is too high, the wear of the diamond segment matrix will be accelerated, causing the diamond to fall off prematurely. When the feed rate is too low, the wear of the carcass is slow, and the diamond is not easy to be edged or polished, resulting in increased cutting resistance, increased power consumption, and decreased cutting productivity. Generally, when cutting soft stone or coarse-grained and inhomogeneous stone, large depth of cut and slow feed should be used. Fast feed is suitable for sawing fine-grained and homogeneous stone. In actual operation, the speed of feeding, retracting and exiting the knife should be slow, and the speed during the cutting process should be uniform.
Our Services
1. Fine raw materials are selected for processing, high grade raw materials, imported cobalt powder and high-quality diamond single crystals, to ensure the best performance of our products.
2. Customized designs are available. We can also help customers design and develop new products, and adjust cutting efficiency and lifespan upon your request.
3. Knowledgeable sales representatives are available to reply all inquiries and e-mails within 24 hours.
4. Every details will be confirmed with you before production;
5. Each processing would be completed by our skillful worker.
6. Strict quality management system. During the whole production process, from raw material choosing, processing to packing, our quality assurance people will strictly control each single and every process to guarantee quality standards and punctual delivery.
7. Detailed and clear pictures will be sent before packing and loading for you.
8. We will keep you update of the order and shipping status till you get the products smoothly.
9. One-stop solution and service for your requirement to save your money and time.
Contact Us
If you’re interested in Diamond Segments for Granite Cutting, please feel free to contact us, (E-mail: [email protected] Phone/WhatsApp: 0086-15805032000 or filling out the form below) we will keep providing quality products and excellent service for you.